$4M
3
2
approved US patents
10K tpa
plant design & engineering works in progress
5 years
until full implementation of easily scalable plant
Through an intensive five-year R&D effort, we have succeeded in developing and patenting a revolutionary technology that provides cutting-edge methods for obtaining titanium metal powder with far fewer carbon emissions.
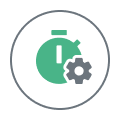
Significant reduction in titanium parts production time
Powder metallurgy or additive technologies utilizing Velta Ti Process powder eliminates long and complex way of obtaining and transforming titanium sponge into the final parts.
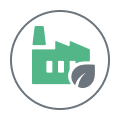
Compliance with “green production” criteria
No solid waste and Zero Liquid Discharge approach. Significantly reduced carbon footprint. Transforming all generated waste into high-added value by-products.
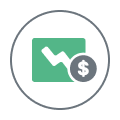
Lower-cost titanium parts production
The industry’s average buy-to-fly ratio for the titanium parts production using Kroll’s sponge is 10:1. When using Velta Ti Process powder with powder metallurgy or additive technologies, the ratio is 1.5:1.
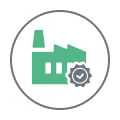
Manufacturing of any types of high-quality alloys and intermetallides
Especially those that are currently either difficult or even impossible to manufacture in industrial quantities.
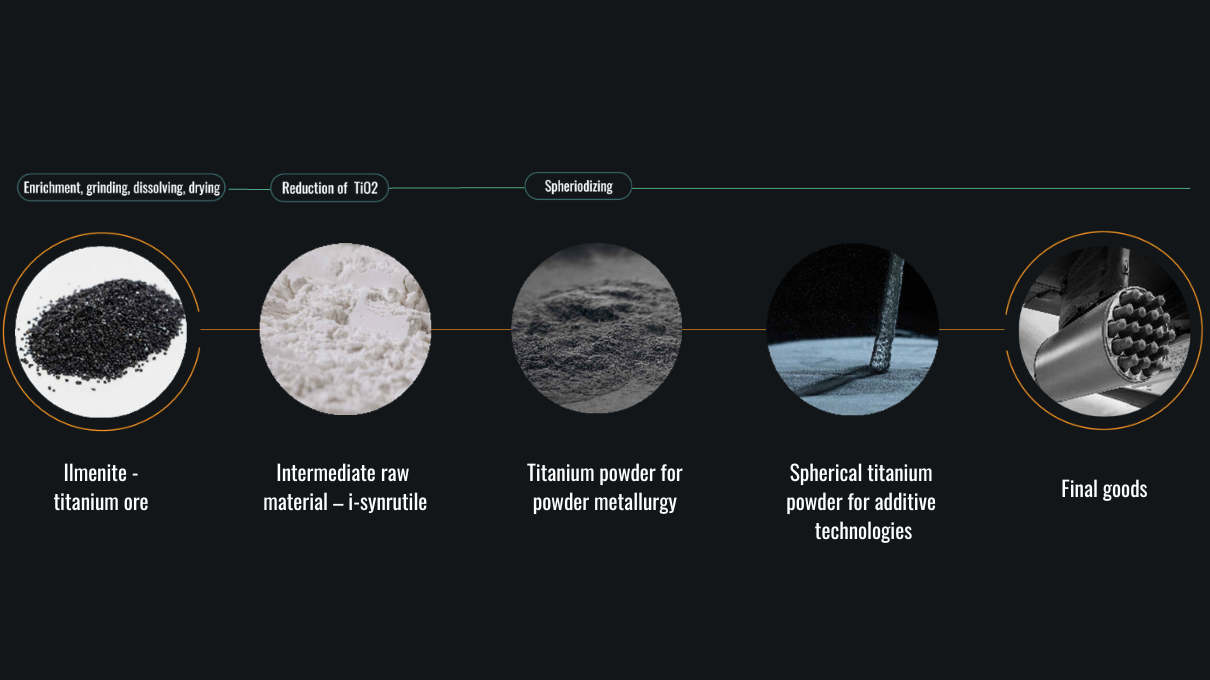